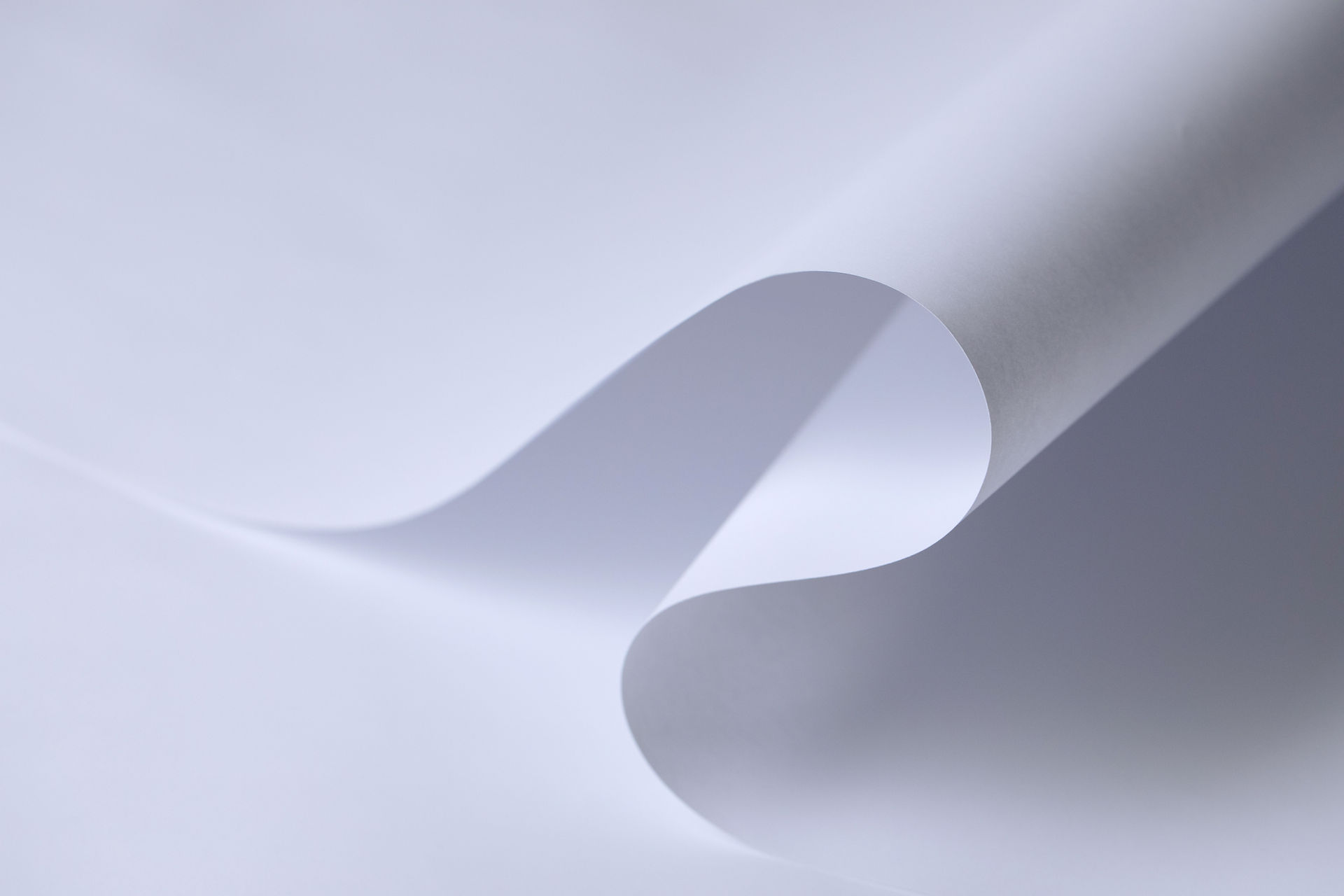
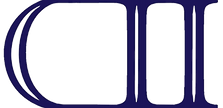
CONTINUOUS
IMPROVEMENT
INSIGHTS

Greg Eckhart
Founder, Owner, Consultant
My Story
Since graduating from Michigan Technological University in 2000, I have been fortunate to have had a diverse and enriching career. My first professional experience was with Delphi Automotive Systems' airbag plant in Vandalia, Ohio. Although now shuttered, at the time it was a huge plant producing airbags and other interior components for some of the most popular GM models of the era. Most notably, the plant had an outstanding industrial engineering team and, in retrospect, did an impressive job of applying Lean principles such as cellular manufacturing, kanban, and single-piece flow. It was there - as a production supervisor - I received my first exposure to the idea of continuous improvement and its benefits.
In 2002, I joined the operations team at the Lear Corporation interiors plant in Wauseon, Ohio. After a short tenure as a production supervisor, I moved into the continuous improvement group as a Six Sigma Black Belt. Lear was much more focused on Six Sigma methodologies than on Lean at the time, which was exciting because it gave me an opportunity to not only learn an entirely new skillset but also teach and apply the Lean skills I had gained at Delphi in this new arena. We had a great team of Black Belts who really enjoyed challenging and learning from one another. Several of them are still friends today.
After several years as a full-time Black Belt at Lear Corporation, I was given the opportunity to become a Six Sigma Programs Manager for the Michigan Manufacturing Technology Center, a not-for-profit consulting group in Plymouth, Michigan. As any teacher will tell you, there is no greater incentive to becoming an expert in a subject than being called upon to teach it to others! This experience, then, is where my technical capabilities in Six Sigma methods - particularly statistical tools - truly matured. My students were excellent and almost all capable engineers and professionals in their own right. They challenged me constantly with their tough questions and I like to think we were all better off for the experience. While primarily focused on small-to-mid-sized manufacturers, MMTC also worked with companies from every sector, even including healthcare and banking. All told, I trained over 160 Black Belt candidates from over 80 different companies during my six years at the MMTC. Not only that, but I also worked with an excellent team of consultants and trainers who helped me grow in other areas as well. Looking back, my years at MMTC were the most formative of my career and an irreplaceable experience professionally.
In 2011, my long commute and consulting lifestyle began to take its toll on my young family, so I decided to accept a position as a Plant Lean Leader at Parker-Hannifin's Hydraulic Filter Division (HFD) in Metamora, Ohio. Again, I found myself in an excellent situation professionally. The plant had been an AME Excellence Award winner in 2010, so already had a track record for Lean excellence. Again, I was afforded an excellent opportunity to offer my contribution to an outstanding organization and help build on their past successes. Later, I would take on the role of Value Stream Manager in which I had operational responsibility for roughly half of the facility. My team and I found dozens of ways to apply continuous improvement principles to our processes and met with a great deal of success.
After Parker, I spent about a year at International Automotive Components (IAC) again in Wauseon, Ohio as their Programs and Continuous Improvement Manager. More focused on program management than CI, it was an eye-opening experience to say the least. We worked with five different automotive OEMs on launches in various stages of maturity. It was exciting work and provided me with exposure to program management and product development, but was not what I was looking for professionally.
I then spent a short time with Sunrise Windows in Temperance, Michigan. Reunited with some of my former colleagues from Parker, I took the role of Quality Manager at the vinyl window manufacturer. Again, I was fortunate to have great group of people to work with and an extremely supportive environment for change and improvement. I also learned a great deal about the window industry and its unique challenges.
However, in 2016 I was given the opportunity to work for Haas Door Company in Wauseon, Ohio as their Quality and Continuous Improvement Manager. This family-owned garage door manufacturer is just a great company. At Haas I learned just how important a positive culture can be and I cannot say enough good things about how the owners treat people - employees, customers suppliers, and even the local community. At Haas Door, I managed projects of all sizes, from simple improvements around the plant to moving entire departments into a new facility. I was also responsible for quality system compliance, including for the ISO 17025-accredited testing lab. I am proud to say we did not have a single external audit finding in my seven years there. Most of all, Haas Door provided me the trust, flexibility, and resources to experiment with some very ambitious projects, many of which I am extremely proud of.
As they say, however, "the one constant is change" and so 2023 I decided to create Continuous Improvement Insights as a way to try a new path and to offer my knowledge and experience to my clients. I look forward to making their businesses better together!